Не забывали мы и бытовые потребности: изготавливались мебель различного назначения, металлическая посуда, репродукторы для радиотрансляционной сети и т. д. А наша лаборатория выпускала даже некоторые медикаменты, например стрептоцид.
К этому же времени был построен цех металлоконструкций производительностью в 16 тыс. т в год. Согласно постановлению СНК СССР цех был передан Стальконструкции Наркомстроя, но поставлял конструкции исключительно для нас. В дальнейшем этот цех был реконструирован и уже как завод переведен на машиностроительный профиль. Важное значение имели ремонт и восстановление Потанинского кирпичного комбината общей производительностью до 60 млн. штук кирпича в год и создание собственных лесозаготовительных участков, с которых уже в 1942 г. мы получили 112 тыс. куб. м древесины.
Характерным для коллектива строителей Челябметаллургстроя было то, что никто из руководителей даже крупных строительно-монтажных подразделений не считал для себя зазорным на время (иногда и длительное) переключаться на маленькое, но решающее на данном этапе успех строительства дело. Так, к весне 1943 г. строительство, получавшее с одного Потанинского завода (вблизи Челябинска) стеновой материал, оказалось в совершенно критическом положении. Панели и блоки в тот период нигде, включая Челябметаллургстрой, не производились, да и проектов зданий из этих рациональных элементов еще не было, и стройке буквально грозила остановка из-за недостатка кирпича. Начальник крупного строительного управления Прокатстроя Дмитрий Семенович Захаров, закончивший к тому времени строительство прокатного цеха, сам взялся за это, по существу, вспомогательное производство и сумел в исключительно короткие сроки достроить новый Потанинский кирпичный завод, интенсифицировать производство кирпича на существующем оборудовании. Уже в мае мы получили с этих заводов 1 млн. штук кирпича, в июне — 3 млн. штук и в июле — около 6 млн. штук кирпича, полностью разрешив проблему со стеновым материалом.
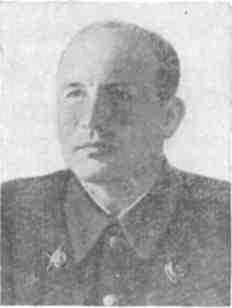
Д. С. Захаров
Вскоре возникла новая проблема — недостаток бензина для нашего автотранспорта, так как жидкое горючее в основном шло на нужды фронта. Мы оказались под угрозой остановки всего автотранспорта, а значит, и строительства. Было принято решение в массовом порядке собственными силами переоборудовать машины на газогенераторное горючее (древесные чурки и другие лесоотходы). Газогенераторы, конечно, изготовляли сами в наших мастерских. Только это и позволило не останавливать строительство практически ни на один день, обеспечить работу автотранспорта. Нас тогда так волновал и занимал вопрос о переоборудовании автомашин на газогенераторы, что я, отнюдь не являясь специалистом в этой области, написал даже статью по этому вопросу, опубликованную в № 7—8 журнала «Строительная промышленность» за 1943 г.
Проектирование основных, вспомогательных и обслуживающих цехов велось непосредственно на площадке строительства филиалом Гипромеха почти одновременно с их сооружением. Это позволило осуществить оперативную увязку работы проектировщиков и производственников и значительно сократить число деталировочных чертежей.
Проект организации работ ограничивался составлением схем, производственно-технических показателей и пусковых пообъектных графиков. Иногда проекты организации работ разрабатывались в нескольких вариантах, чтобы в зависимости от создавшихся в данный момент условий можно было быстро предложить производству готовое решение.
Заниматься проектированием объектов первой очереди, а также подготовительными и вспомогательными работами, не приступая к основным цехам металлургического завода, мы могли только в течение 2—3 месяцев. Дальнейшее создание производственных предприятий могло вестись только параллельно с основными работами.
К 1-й очереди основных объектов металлургического завода относились: электросталеплавильный цех, по мощности в то время самый крупный в Европе (5 печей по 30 тыс. т стали в год), прокатный цех длиной около 500 м, чугуно-меднолитейный, кузнечный и ремонтно-механический цехи, завод огнеупоров и деревообделочный цех.
Площадь кровли основных и вспомогательных объектов составляла 70 тыс. кв. м. Из них 42 тыс. кв. м настилались по деревянным сегментным фермам, изготовляемым под открытым небом. Число ферм достигало 500 при пролетах от 15 до 25 м.
Деревянные фермы обшивались двумя слоями досок. Металлические фермы перекрывались сборными железобетонными плитами. В тех отсеках, где избыточные тепловыделения вызывали опасность в пожарном отношении, применялись решетчатые металлические фермы с холодным деревянным покрытием. Пожарные зоны, а также потолки в местах установки печей подшиты кровельным железом.
Исходя из реальных возможностей получения металла и металлоконструкций для основных цехов были приняты следующие конструктивные решения.
Электросталеплавильный цех, имеющий высоту до 25 м, пролета до 26 м и шаг колонн до 18 м, оборудован мостовыми кранами грузоподъемностью до 75 т. Значительные размеры цеха и большая мощность кранов обусловили выбор металлических конструкций для наиболее ответственных несущих элементов. Менее нагруженные колонны и фахверки сделаны железобетонными, а некоторая часть ферм — деревянной.
Общий вид электросталеплавильного цеха
Обычно применявшаяся металлическая конструкция рабочей площадки заменена в большей части железобетоном. Последний пролет — обдирочный — выделен в отдельное здание. При строительстве этого здания было использовано 914 т (около 20%) металлоконструкций, демонтированных с других предприятий, оставшихся на территориях, временно захваченных врагом.
Подкрановые балки при шаге колонн 6 м конструировались железобетонными; в тех местах, где шаг увеличен до 12 м и более, а также в пролетах, оборудованных быстроходными мостовыми кранами, установлены металлические подкрановые балки. Все железобетонные конструкции — колонны, подкрановые, обвязочные и фундаментные балки — сборные; их вес не более 10 т, и потому монтаж обеспечивался наличным крановым оборудованием.
Недостаток некоторых материалов и сжатые сроки строительства заставляли нас по согласованию с проектировщиками идти на ряд упрощений, но отнюдь не в ущерб технологическому процессу или прочности сооружений. Например, в горячих цехах — прокатном, электросталеплавильном, ремонтно-кузнечном и чугуно-меднолитейном — полы были глиноземлебитные из тщательно утрамбованных сапролитов и суглинков, являвшихся основными грунтами строительной площадки; в слесарных мастерских, моторных помещениях, ремонтно-механическом и деревообделочном цехах — из местной дресвы, пропитанные смолой и тщательно укатанные. Дресвяные полы прочны, эластичны, нетеплопроводны, имеют сравнительно гладкую поверхность.
Для облицовки боровов коксовых печей, сушки магнезита, а также при кладке известково-обжигательных и других вспомогательных печей был применен вместо дефицитного огнеупорного — трепельный кирпич, сохраняющий согласно результатам лабораторных испытаний огнестойкость при температуре до 1300°. Намеченная проектом постройка двух больших и сложных зданий главного распределительного устройства и щита управления при ТЭЦ объемом 12 тыс. куб. м и стоимостью 700 тыс. руб. заменена одноэтажным зданием стоимостью около 500 тыс. руб. Этим была обеспечена своевременная подача электроэнергии пусковым цехам, что позволило повременить со строительством капитальных сооружений по крайней мере один год без ущерба для нужд эксплуатации.
Для экономии металла некоторые трубопроводы были заменены бетонными и асбоцементными. Вместо общезаводской ливневой и производственной канализации выпуск в кюветы производственных вод был осуществлен по закрытым деревянным лоткам.