Электросварку впервые в мире применил русский изобретатель Н. Н. Бенардос в 1882 году, а его способ усовершенствовал несколько позже другой изобретатель — Н. Г. Славянов. У электросварки большие преимущества перед клепкой и другими способами соединения деталей. Возьмем, к примеру, клепку корпуса парохода. Она была невозможна без применения множества соединительных угольников, стыковых планок, стальных прокладок. Уйму металла и средств тратили на изготовление этих вспомогательных деталей. При электросварке они все не нужны. А сколько металла и труда затрачивалось на клепку! Например, при постройке арктического ледокола в его корпус забили до миллиона заклепок. И для этого потребовалось просверлить два миллиона отверстий в деталях корпуса. При электросварке не надо ни отверстий, ни заклепок. А сколько времени и средств отнимало уплотнение заклепочных швов, или, как его называют, чеканка. Сварной шов не требует этой работы, он гораздо прочнее и плотнее заклепочного шва. Клепку выполняла целая бригада из трех и даже четырех рабочих. А при электросварке работает один рабочий.
Представляете теперь, сколько сберегает электросварка металла, рабочей силы и денег?
Еще быстрее и прочнее сваривают части корпуса парохода сварочными автоматами. Чаще всего встречается сварочный автомат «Трактор». Только не подумайте, что это настоящий трактор. Таким тракторов землю не вспашешь, — он слишком маломощный. Не одолеет он и большого уклона. Да и по размерам и устройству он мало похож на настоящий трактор. Зато стальные детали он сваривает замечательно.
Сварочный автомат «Трактор». 1 — самоходная тележка; 2 — электромотор; 3 — кабель; 4 — сварочная головка; 5 — сосуд с флюсом; 6 — щит управления; 7 — катушка с электродной проволокой; 8 — электродная проволока.
Вот сварщик установил вдоль стыка двух листов палубы небольшую самоходную тележку. На тележке смонтированы части автомата. Тут и маленький электродвигатель, и пост управления, и сосуд с флюсом — пескообразным веществом, и сварочная головка, сквозь мундштук которой пропущен конец электродной проволоки, намотанной на катушку. Самая хитроумная часть автомата — сварочная головка. Она, как говорят, мастер на все руки: возбуждает электрическую дугу, непрерывно подтягивает к месту сварки электродную проволоку, сматывает ее с катушки. И самое главное — она не дает дуге менять свою длину, а это очень важно для качества сварки. Вот сварщик нажал кнопку на посту управления. Тележка плавно покатилась вдоль стыка. Кончик проволоки коснулся стыка деталей, возбудилась электрическая дуга. Ее сразу же покрыл слой флюса, который непрерывно сыплется из сосуда. Дуга становится невидимой под пузырем из расплавленного флюса. Она горит внутри этого пузыря — среди паров расплавленного металла и флюса. Флюс — замечательное вещество. Он отлично защищает сварной шов от вредного влияния азота и кислорода воздуха. При сварке под флюсом почти все тепло дуги идет на сплавление кромок деталей. При ручной сварке много тепла рассеивается в воздухе и металле. А какая большая разница в скорости ручной и автоматической сварки! Говорить об этой разнице — все равно что сравнивать скорость пешехода и автомобиля. Но автомат «Трактор» — весом около 70 килограммов — аппарат громоздкий. Им нельзя, как при ручной сварке, варить в любом положении и в самых тесных местах. Не может он варить короткие и криволинейные швы. И вот ученые изобрели в 1948 году новый аппарат — шланговый полуавтомат. У него тоже есть тележка. Но только она не самоходная. На ней механизм для подачи электродной проволоки к месту сварки.
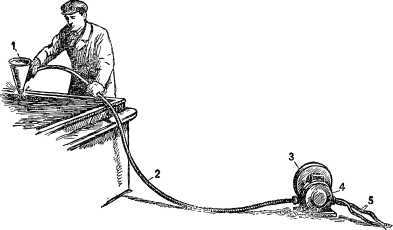
А это сварочный полуавтомат. 1 — сварочный наконечник с рукояткой и воронкой для флюса; 2 — гибкий шланг; 3 — катушка с электродной проволокой; 4 — подающий механизм, 5 — кабель.
Электродная проволока сматывается с катушки и проталкивается подающим механизмом сквозь гибкий шланг к наконечнику, находящемуся у сварщика в руках. Все остальное совершается, как у автомата «Трактор». Разница в том, что сварщик передвигает наконечник с концом проволоки и сосудом для флюса вручную, а у автомата все механизировано. Поэтому шланговый аппарат называют не автоматом, а полуавтоматом.
Шланговыми полуавтоматами можно варить в таких местах, которые недоступны автомату «Трактор», и быстрее, чем ручной сваркой. Но швы, идущие вверх или над головой, — как говорят, вертикальные и потолочные, — варить ни полуавтоматом, ни автоматом нельзя. Тут уже и в особо тесных местах поле деятельности до сих пор остается за ручной электросваркой.
Но все же ученые считают, что и это ненадолго.
Электросварка совершила полный переворот в судостроении. Она сильно изменила и упростила конструкцию корпуса парохода. Она намного сократила число операций по изготовлению деталей. Наконец, электросварка помогла разработать новые способы скоростной постройки судов.
Скоростное строительство
Еще двадцать лет назад техника постройки парохода была невысокой. Тогда корпус на стапеле собирали из многих тысяч отдельных деталей и узлов. Из множества ребер, подаваемых по очереди, составляли скелет корпуса. Потом на скелете собирали оболочку, опять-таки из отдельных листов наружной обшивки и палуб. Все части корпуса соединяли заклепками. Условия работы были трудными. Вес машинки для сверления дыр достигал 30 килограммов, а клепального пневматического молотка — 16 килограммов. Такой инструмент приходилось держать на весу, часто изгибаясь в три погибели в тесных отсеках. Барабанные перепонки рабочих лопались от страшного звенящего грохота, а легкие человека разъедались дымом от горнов для подогрева заклепок.
Работы шли так: пока судосборщики не соберут тот или иной район корпуса, нельзя работать сверловщикам. А пока не закончили свою работу сверловщики, здесь нечего делать клепальщикам. После клепальщиков приходили на стапель чеканщики. Их дело — обеспечить плотность заклепочных швов и испытать корпус парохода на водонепроницаемость. Металл уплотняли особым инструментом — чеканом, а испытывали так: нальют в отсек воды и смотрят снаружи, — нет ли течи в заклепочных соединениях. Если в каком-либо месте просочилась вода, — это место подчеканивали еще раз. Последними приходили на пароход маляры. Они красили испытанные отсеки. Рабочие других специальностей — судомонтажники, электромонтажники, плотники, столяры — приступали к работе только после спуска парохода на воду. Со стапеля сходили в воду пустые корпуса, без механизмов, устройств и оборудования.
Всем этим «начиняли» пароход во время достройки на плаву. Такая постройка тянулась долго — по нескольку лет. С такими темпами нельзя было мириться.
Рабочие и инженеры совместно с учеными взялись за улучшение техники судостроения. И был произведен настоящий переворот. А натолкнул судостроителей на этот переворот новый способ постройки жилых домов. Прежде дома строили по кирпичику. Потом их стали собирать из готовых крупных блоков вместе с оконными рамами и другим оборудованием. Здание растет теперь, словно гриб, — не по дням, а по часам.
Примерно то же произошло и с постройкой парохода. Судостроители рассудили так: нельзя ли уподобить пароход дому? Как бы разбить днище, борта и палубы парохода на большие куски — секции? Как бы эти секции изготовлять заранее в цехе в удобных условиях, а потом быстро собирать из них на стапеле корпус парохода? Так и сделали. Затем секции стали объединять в более крупные куски парохода — блоки.
Из секций собирают блок.
Блок — это уже полновесный кусок корпуса — от борта до борта и от днища до палубы. В сборочно-сварочном цехе завода можно увидеть целую носовую или кормовую оконечность парохода, а также многоэтажную надстройку с палубами, переборками, фундаментами под механизмы, трубопроводами, разными устройствами и даже с оборудованными помещениями. Вес такого куска достигает 100 тонн и более. Тут же стоят огромные днищевые и бортовые секции длиною по 20 метров. Это означает, что теперь корпус собирают не из многих тысяч отдельных деталей и узлов, а из нескольких десятков секций и блоков. Для небольшого судна нужно изготовить только 5–6 блоков. Прежде, до спуска парохода на воду, можно было заранее заготовить для следующего только детали и небольшие узлы. Теперь к моменту спуска одного парохода корпус другого уже фактически готов в виде его огромнейших кусков — секций и блоков. На стапеле остается только сварить их в одно целое.