Resistance coefficient in the open position, not more than 0.2.
Dampers are available in the following types:
• Air unified;
• Round section with electric drive;
• Rectangular cross-section with electric drive;
• Circular cross section with manual drive;
• Rectangular cross-section with manual drive;
Air dampers are designed to regulate the amount of air and are used in air ventilation systems, air heating and other sanitary systems with an operating pressure of up to 1000 Pa.
Questions to Chapter 5
1. For what purpose are air distribution devices used?
2. Name the main characteristics of air distribution devices.
3. What factors are taken into account when choosing the type of air distribution device in the room?
4. What is the value of the dynamic pressure required for the operation of the lobe check valve?
5. What is the purpose of electric heating of air dampers, in which cases it is used?
Chapter VI. Mounting tools, fixtures and accessories for mechanization of installation work
Installation of ventilation systems is carried out by a team. As a rule, the integrated team of ventilation fitters includes two or three people with related specialties of an electric welder and a gas cutter. The numerical composition of the team is usually six to seven people. Each team is provided with a set of tools, which allows the team or its units to independently perform almost the entire scope of work on the installation of ventilation systems.
Table 6.1.
Table 6.2
Recommended set of electric welding equipment and tools for a team of locksmiths – ventilators
Table 6.3
Tools for gas cutting of steel
Table. 6.4.
Basic data of non-self-propelled inventory means of scaffolding and rigging
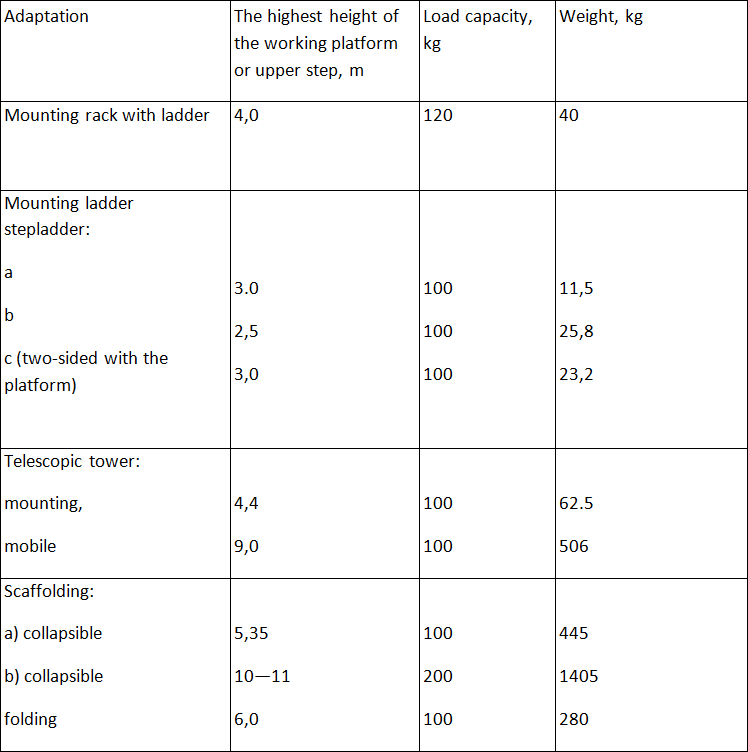
The connection of the end of the box with the flange is carried out using a TRUMPF TF 350–2 manual press. The fastening element is a "press rivet", which is cut and molded from the material of the workpiece in one working stroke of the punch (punch). This mechanical process of joining metal sheets is known as "offset connection" – the upper sheet is connected to the lower by kinematic closure. Its main advantage over traditional spot welding is that there is no damage to the surface due to heating, the butt joint is corrosion resistant. The TF 350–2 press is designed both for joining uncoated sheets and galvanized, painted, polymer-coated sheets. Preliminary and final processing with such "cold welding" is not required, there are no costs for screws, rivets and other connecting elements. For ease of operation, the punch, which forms the "rivet" with a continuous pressing blow, is installed in a movable lever. Thus, the tool frame can be "opened" with a single movement of the hand in order to easily and quickly install the tool at the desired point of the tire. At the same time, the flange height is allowed up to 40mm. A special cone puller makes it possible to fasten the tire with the box as close as possible to the edge of the duct. Depending on the technical and aesthetic requirements, the connecting element can be concave into the surface of the box or protrude above the surface. It is possible to obtain an almost airtight connection for sheets of various thicknesses by choosing the appropriate matrix size. A set of tools is installed on the TRUMPF TF 350–2 press, in accordance with the specified total thickness of the sheets. Tool change is quick and easy and does not require special tools or skills. The productivity of the TRUMPF TF 350–2 press is 2 rivets per second. The tool is suitable for both portable and stationary applications.
Seam connection. The Pittsburgh fold is an ideal connection method for straight or curved boxes. A smooth, dense and aesthetic connection is obtained without any additional processing when using TRUMPF F 300 series tools. The Pittsburgh fold ("American") is obtained by continuous roller running-in, without damaging the surface and coating. Automatic feed control guarantees seam accuracy and uniform joint density. TRUMPF folding machines are suitable for both straight boxes and bends, with a minimum internal radius of only 300 mm.
To install grilles, blinds, valves and air conditioners themselves, it is often necessary to make cutouts in an already mounted box. Especially for this application, TRUMPF has developed the C 160 slotted scissors, which allow you to make cutouts with great accuracy, without deforming the sheet, and the chips do not get inside the box, because they stand out above the surface of the sheet with a continuous tape. You can start and finish the cut at any point on the surface of the box; by turning the small handle on the cutting head, the chips are bitten off at the desired point. The edge of the cut is perfectly smooth. These scissors can be used to cut welded spiral seams on round ducts up to 2.5 mm thick.
Questions to Chapter 6
1. Name the composition of the joint team of locksmiths.
2. Explain the principle of operation of the instrument from the main set (one, at the student's choice).
3. Describe the method of connecting the flange to the end of the duct.
4. What is the reason for the location of the connecting element relative to the duct?
5. What are the advantages of a folding connection?
Chapter VII. Installation of ventilation equipment
The production of installation ventilation works at facilities implies preparation for the installation of ventilation equipment, which requires careful preparatory work. Special attention should be paid to the reality of the implementation of design solutions by the installation team, both technically and in terms of execution.
7.1.Projects of production of works
The project of work production is the basic guide for the organization and production of installation work at the facility. Project of work production helps to plan all the preparatory work, including the execution of orders for air ducts and applications for ventilation equipment and materials, to determine the storage locations of bulky ventilation parts. The project of work production contributes to the uninterrupted conduct of installation work, improving the quality of installation.
The complete project of work includes the following sections:
1) situational master plan, usually on a scale of 1:400, with reference to the storage locations of air ducts and ventilation equipment and an intra-building transport scheme;
2) schematic plan of the object with drawing of axes and locations of ventilation equipment;
3) list of ventilation equipment supplied by the customer;
4) characteristics of air ducts for ventilation systems and a list of installation drawings or sketches on them;