Цель этой главы. Цель этой главы – указать на наличие стабильной системы возникновения проблем на промышленном предприятии и объяснить, почему, когда система стабильна, за повышение качества ответственен менеджмент. Дополнительные примеры вы найдете в последующих главах.
Немного «народной мудрости». В Америке распространено мнение, что качество и объемы производства несовместимы, – вы не можете иметь и то и другое одновременно. Руководитель предприятия, скорее всего, скажет вам, что это ситуация «или−или». Он давно пришел к выводу, что если повышается качество, то объем производства начинает падать. Если же увеличивается объем производства, то страдает качество. Все дело в том, что этот руководитель не знает, что такое качество и как его добиться[4].
Ясный и убедительный ответ на мой вопрос: «Почему растет производительность, когда повышается качество?» – я получил от 22 промышленных рабочих на встрече со мною:
Лучше не скажешь. Часто встречается другой вариант ответа:
Качество для производственного рабочего – это прежде всего возможность получать удовлетворение от работы, гордиться своим мастерством.
Повышая качество, мы превращаем бесцельно расходуемые человеко-часы и не полностью использованное машинное время в отличную продукцию и превосходные услуги. В результате возникает цепная реакция – снижаются затраты, повышается конкурентоспособность, люди на производстве чувствуют себя более счастливыми, рабочие места преумножаются.
Четкое определение соотношения качества и производительности дал мой друг доктор Ёсикасу Цуда из Университета Риккё в Токио в письме, которое он написал мне из Сан-Франциско 23 марта 1980 г.:
«Я только что вернулся с Северного полушария, побывав за год в 23 странах, где посетил множество промышленных предприятий и пообщался со многими специалистами.
В Америке и Европе люди теперь больше интересуются затратами на качество и системами аудита качества. Но в Японии мы прежде всего стремимся улучшать качество с помощью ваших методов… Когда мы улучшаем качество, мы повышаем и производительность, а это как раз то, что Вы предсказывали нам в 1950 г.».
Доктор Цуда говорит, что западная промышленность стремится повышать качество, но не превышая уровня, который на основании полученных данных представляется экономически эффективным. Кто-то поинтересовался: «Насколько мы можем снизить качество, не теряя потребителей?» Этот вопрос – верх непонимания проблемы. И это типичная реакция американского менеджмента. В противовес этому японцы упорно идут вперед и улучшают процесс, не глядя на цифры. Так они повышают производительность, снижают затраты и завоевывают рынки.
Пробуждение Японии. В 1948 и 1949 гг. руководители некоторых японских компаний сделали открытие, что повышение качества естественно и неизбежно ведет к росту производительности. Это наблюдение стало результатом работы группы японских инженеров, которые изучали литературу по контролю качества, полученную от специалистов Bell Laboratories, работавших в штате оккупационной администрации генерала Макартура. Среди книг была работа Уолтера Шухарта «Экономичный контроль качества производственных изделий» (Economic Control of Quality of Manufactured Product. Van Norstrand, 1931; репринтное издание American Society for Quality Control, 1980). Результаты были поразительными и показывали, что производительность действительно повышается при снижении вариации, именно так, как пророчествовали методы и логика книги Шухарта. Визит иностранного эксперта летом 1950 г. (Так д-р Деминг говорит о себе. – Прим. пер.) инициировал в Японии цепную реакцию повышения качества, ставшую их образом жизни[5]. Схема этой цепной реакции висела на доске во время каждой нашей встречи с высшим руководством в Японии начиная с июля 1950 г. (см. также рис. 1).
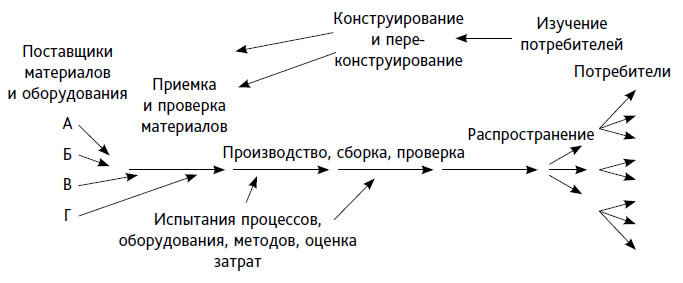
Рис. 1. Производство рассматривается как система. Повышение качества охватывает всю производственную линию от поступающих материалов до потребителя и до проектирования и перепроектирования будущих продукции и услуг. Эта схема впервые применена в августе 1950 г. на конференции с высшим менеджментом в отеле de Yama на горе Хаконэ в Японии. В организации сферы услуг источники А, Б, В и т. д. могут обозначать источники данных, такие как выставленные счета (в универмаге) или результаты работ на предыдущих операциях: выписка счетов, прием вкладов, снятие денег со счетов, учет поступления и расхода запасов, выписка накладных на отгрузку и т. д.
Производственные рабочие в Японии, как и во всем мире, всегда знали об этой цепной реакции, знали они и о том, что дефекты и погрешности, которые видны потребителю, ведут к потере рынка и могут стоить им места.
Как только японский менеджмент постиг смысл этой цепной реакции, все жители страны начиная с 1950 г. обрели общую цель, и имя ей – качество.
Поскольку и кредиторы, и акционеры не оказывали давление на менеджмент с целью получения высоких дивидендов, усилия, направленные на повышение качества, стали узами, связывающими менеджмент и производственных рабочих. В Японии не было недружественных поглощений и скупки акций на заемный капитал. Менеджеров не оценивали по критерию «цена/доход на акцию». Поэтому японские руководители могли придерживаться постоянства цели (см. пункт 1 во второй главе, раздел «Подробное описание 14 пунктов»). (Цитаты из статей Цуруми и Кауса из главы 3 здесь тоже вполне уместны.)
Блок-схема (рис. 1). Мало просто говорить о качестве. Нужно что-то делать. Блок-схема (диаграмма потоков) на рис. 1 указывает направление действий. На схеме материалы и оборудование поступают слева. Повторю, что качество исходных материалов нужно улучшать. Работайте со своим поставщиком как с партнером, выстраивая долгосрочные отношения, основанные на лояльности и доверии, для повышения качества исходных материалов и снижения затрат.
Потребитель – самое важное звено производственной линии. Качество следует нацелить именно на его нужды, настоящие и будущие.
В основе улучшений лежит позитивное намерение менеджмента. Это намерение должно стать очевидным для инженеров и всех остальных работников завода, кто устанавливает технические условия, проводит испытания, управляет процессами. Излагаемые здесь принципы в совокупности с цепной реакцией, описанной выше, блок-схемой на рис. 1 и методами, которым обучены сотни инженеров, легли в основу трансформации японской промышленности (подробнее см. приложение). Так началась новая экономическая эра.
Менеджмент осознал свою роль в улучшении каждого процесса. Инженеры овладели простыми, но мощными статистическими методами, позволяющими установить наличие особых (специальных) причин вариации, и поняли, насколько важно непрерывно совершенствовать процессы (пункт 5). Улучшение качества стало общей целью:
– в масштабах всей компании: для всех заводов, менеджеров, инженеров, производственных рабочих, поставщиков – всех без исключения;
– в национальном масштабе.
Улучшение качества охватывало все процессы на производстве и в обслуживании – закупки, проектирование и перепроектирование продукции и услуг, инструменты и приспособления, производство, маркетинговые исследования.
Должна ли страна быть бедной? Фактически в 1950 г. Япония имела отрицательный платежный баланс. В стране нет природных ресурсов – нефти, угля, железной руды, меди, марганца, даже леса. Более того, Япония имела широко известную репутацию производителя бросовой продукции и была вынуждена экспортировать товары в обмен на продукты питания и оборудование. Вырваться из этого порочного круга можно было, только повысив качество. С этого момента потребитель становится самым важным звеном производственной линии (рис. 1). Это был серьезный вызов высшему менеджменту Японии.